寶馬第一輛純電動i3已經(jīng)在今年九月十八日駛出了位于德國萊比錫工廠的生產(chǎn)線,這款緊湊型掀背電動車是寶馬公司最新打造的i系列中的一個車型,而i系列所有車型都將采用電力驅動系統(tǒng)。寶馬為我們帶來的i系下一款車型將會是i8插電式混合動力跑車,但它會在德國其他的工廠進行流水線組裝工作。
寶馬i3上科技含量最高的要數(shù)碳纖維增強復合材料(CFRP)車身,這種材料是由寶馬公司和西格里公司(SGL Group)聯(lián)合開發(fā)的,以基于聚丙烯腈的熱塑性紡織纖維為原材料,在一定的壓力和溫度下,轉化成極其細長的碳纖維絲線,其中每條碳纖維的直徑僅有0.007毫米,最后再經(jīng)過相應的氧化和碳化處理,形成車身材料。
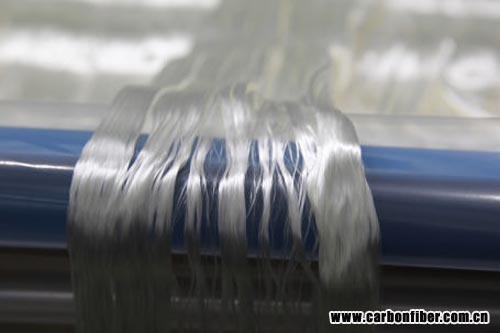
每條聚丙烯腈線束包含100000根白色細絲,方便生產(chǎn)兩條各50000根絲線的碳纖維束 123,123
最初加工出的碳纖維細絲是以線束的形式呈現(xiàn)在我們面前的,而每條線束都含有上萬條絲,所以還需要對它們進行纏繞在線軸上的后續(xù)處理,為之后的裝運工作做好一切準備。值得一提的是,西格里工廠生產(chǎn)碳纖維的整個過程非常環(huán)保,因為他們所消耗的電能全部來自哥倫比亞河的水利發(fā)電能量。
碳纖維材料被運往寶馬在德國瓦爾斯多夫的零部件加工廠,然后根據(jù)需要紡織成各種各樣的結構和樣式;再接著工作人員把這些半成品送往萊比錫和蘭茨胡特的碳纖維增強復合材料沖壓車間,完成碳纖維軟性板材(類似坐墊、地毯)的制造。通過各種加工機械,碳纖維板材被切割成各種不同的大小和形狀,然后再利用熱處理或塑料粉末高壓粘合技術,把這些板件加工出立體構型。加工成型階段,每一次三個形狀完全相同的碳纖維板件要重疊在一起,這樣可以有效地降低在最終的樹脂傳遞成型過程中材料發(fā)生撕裂的可能性。
123456
白色的聚丙烯腈變成黑色的碳纖維
樹脂傳遞成型則是把高溫高壓的復合樹脂注射入模腔,浸透增強纖維材料、固化、脫模成型的技術,比傳統(tǒng)高耗時的烘箱固化技術要先進很多。首款寶馬i3成功下線的慶祝儀式上,美國能源獨立協(xié)會(AEI)還被特別邀請來參觀萊比錫工廠。
在過去的十多年時間里,寶馬公司一直致力于碳纖維增強復合材料產(chǎn)品和創(chuàng)新技術的研發(fā),工程師們已經(jīng)把產(chǎn)品的生產(chǎn)周期降低了一半以上,制造和原材料成本也減少了30%—40%。目前工程師又有了進一步縮減碳纖維增強復合材料生產(chǎn)制造周期的新想法,但在i3的實際生產(chǎn)過程中也碰到了不少難題,可工程師沒有為之擔心,因為他們知道這是最終的成功所必須經(jīng)歷的經(jīng)驗積累階段。寶馬的樹脂傳遞成型技術允許加工那些尺寸較小的部件,比如說車身側圍,再把它們粘結成一個更大的組分,最終在模具中結合成整體車身;這種技術把零部件的總數(shù)降低到傳統(tǒng)鋼制車身使用總量的三分之一。
本文來自123
碳纖維軟性板材
寶馬萊比錫工廠所能加工的碳纖維增強復合材料部件的尺寸等級是其它競爭對手望塵莫及的,如此大優(yōu)勢得益于寶馬公司巨大的科研經(jīng)費投入:為生產(chǎn)i3的萊比錫工廠投入4億歐元,生產(chǎn)i系產(chǎn)品的其他工廠6億歐元。那些用于i3車身上但結構較為簡單的部件由蘭茨胡特工廠生產(chǎn),再運送往萊比錫,這樣不同地點同一時間就可以各加工一種部件,減少生產(chǎn)總時間。
樹脂傳遞成型前的剪裁處理
在樹脂傳遞成型階段之后,利用水激光切割技術完成碳纖維增強復合材料部件上的嵌入空和邊緣剪裁加工;接著在最新的全自動化車身車間中,所有部件進行過表面磨砂處理,增加粘附性后,結合為一個穩(wěn)固整體。
本文來自123
兩次沖壓處理:加工成型處理和樹脂傳遞最終成型
裝配車身使用的膠粘劑是寶馬公司與一家大型化工企業(yè)聯(lián)合開發(fā)的,擁有快速硬化的特性,但它的配方至今還是機密。僅僅需要幾秒鐘的時間,膠粘劑就能夠發(fā)揮作用,這樣一個部件連接點在噴涂上膠粘劑后,幾乎不用耗費時間車身就可以移動到生產(chǎn)線下一個膠粘劑噴涂點,粘合下一個連接點。除此之外,在一些核心連接點上還安裝了紅外線輔助加熱設備,進一步縮短固化時間。i3車身上的粘結點線總長度達到了160米。
除了車頂使用了可回收再利用的碳纖維增強復合材料,i3外圍全部采用樹脂塑料,這也是寶馬運用這種材料的首款汽車。相同體積大小下,塑料板材的重量只有鋼板的一般,而且四分之一的樹脂材料還是可再生或可循環(huán)使用的。因為加工設備存在一定的差異,車身外圍塑料板材由三種不同的熱塑性注射成型加工工藝完成,其中最先進的是外圍塑料結構和基底結構同時注射成型和結合成整體的工藝。
本文來自123
高度自動化的萊比錫車身車間
塑料板材的噴漆處理是一件一件完成的,有些部件僅僅需要一層面漆和一層保護層即可,但另外的部件則需要一層底漆。之所以減少底漆的使用,是因為利用傳統(tǒng)的陽離子電泳浸涂底漆工藝,會給車輛增加10公斤的漆面重量;另外萊比錫先進的噴涂車間還節(jié)省了50%的電能消耗和70%的水消耗。說到這就不得不提到,生產(chǎn)i3消耗的所有能量都是由當?shù)氐娘L力發(fā)電機提供的。
車身車間的機器手完成檢查和其他功能
i3搭載的大容量鋰離子電池和采用的鋁質承載結構都是在寶馬丁格爾芬工廠加工生產(chǎn)的,整套承載結構包括160個焊接組分,電池組包括96個三星制造的方形蓄電單元。生產(chǎn)設備把蓄電單元成八個獨立的模塊,通過20個機器手的自動化處理,依次加工出各模塊;然后把這些模塊安裝在高強度鋁材質車體結構中,最后再手工把它們串聯(lián)起來。功率125千瓦的電動機是在寶馬蘭茨胡特工廠生產(chǎn)的,其中定子使用的銅線總長度在2公里左右,以一種特殊的形式纏繞在定子上,來更好地降低總量。蘭茨胡特工廠還加工了i3使用的儀表面板。
內容來自123456
車身模塊與驅動模塊的拼接
i3的車身模塊和驅動模塊(包括承載結構、電池組、電動機、選裝內燃機、懸架等)是在萊比錫工廠由兩條獨立的生產(chǎn)線分別組裝的,然后僅需要十個金屬緊固件就能夠把這兩部分搭配為一個整體,但還需要使用上述的秘方膠粘劑才能實現(xiàn)最終的密封性連接。
現(xiàn)在讓我們把原材料送入車身加工車間,耐心等待二十個小時,你就可以在總裝車間出口見到一輛嶄新的寶馬i3了。
蓋世汽車